Dekorieren mit MD-Folien aus SBC
Neue Verfahren und Produkte werten den Schrumpffolienmarkt auf
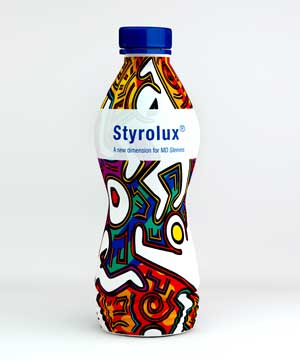
Quelle: Styrolution GmbH
Und der Markt für diese dekorativen Folien wächst weiter. Treibende Kräfte sind steigende Anforderungen an Produktdifferenzierung, Marken-Image und die Menge an Verbraucherinformation sowie der Wunsch einer immer höherwertigeren Präsentation von Endverbraucherprodukten am Point of Sale.
Konkurrenz für TD-Folien
Bislang wird der Markt der dekorativen Schrumpffolien von querverstreckten Folien (TD = transverse direction) beherrscht. Die Technologie des Querverstreckens ist ausgereift und gut etabliert, erfordert aber hohe Investitionen und große Produktionsflächen.
Maschinentechnisch einfacher und entsprechend kostengünstiger ist das Verstrecken in Extrusionsrichtung (MD = machine direction). Das Recken geschieht hier auf einer Strecke mit bis zu 13 Rollen. Auf den ersten Rollen, der Heizstrecke, wird die Folie auf die erforderliche Temperatur gebracht. In der Reckstrecke wird die so erwärmte Folie durch die zunehmende Geschwindigkeit aufeinanderfolgender Rollen bis zur gewünschten Verstreckung gedehnt.
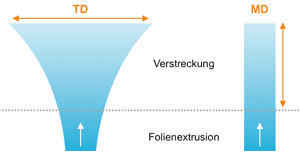
Quelle: BASF
Auf diesen Anlagen, wie sie beispielsweise von Brückner (Siegsdorf) angeboten werden, sind abhängig vom Folienmaterial verschiedene Reckverhältnisse und damit auch unterschiedliche Schrumpfraten erzielbar. Die Investitionskosten für die kompakten MD-Anlagen liegen deutlich unter denen der breiteren und größeren TD-Anlagen.
Auch bei der Verarbeitung können die MD-Folien punkten: Während bei den querverstreckten Materialien in einem separaten Verarbeitungsschritt ein Sleeve hergestellt werden muss, lassen sich die längsverstreckten Folien im sogenannten ROSO-Verfahren (roll on shrink on) direkt von der Etikettenrolle auf die Behälter aufbringen. Die Einsatzmöglichkeiten des wirtschaftlich sehr interessanten MD-Verfahrens waren zunächst allerdings begrenzt. Grund dafür war der niedrige Schrumpfgrad der früher ausschließlich verwendeten PP-Folie von maximal 20 Prozent.
ROSO-Technologie weiterentwickelt
[video nm:20110412-basf-video1]
Um den kostengünstigeren MD-Folien einen breiteren Markt zu erschließen haben die drei großen Maschinenhersteller Krones (Neutraubling), Sacmi (Imola, Italien) und Sidel (Hünenberg, Schweiz) das ROSO-Verfahren in den letzten Jahren weiterentwickelt und damit die Voraussetzungen für die Dekoration auch komplex geformter Behälter geschaffen. Die passenden Rohstoffe zur Herstellung von Folien mit hohen Schrumpfraten bietet z.B. Styrolution GmbH, eine Tochtergesellschaft der BASF in Ludwigshafen, an.
Ausgangspunkt und im Markt weitverbreitet ist ein Verfahren, bei dem die Folie direkt auf die Flaschen aufgerollt, die Folienenden durch UV-härtenden Kleber gehalten, verbunden und die Folie zur weiteren Fixierung auf den Behälter aufgebürstet wird. Die Verklebung auf der Flasche sowie das Arbeiten mit Bürstensystemen bringt allerdings gewisse Einschränkungen bezüglich der Flaschenform mit sich. Extreme Radienunterschiede bzw. Schrumpfraten von über 60% sind auf diese Weise nicht realisierbar.
Bei alternativen Verfahren wird die Folie zunächst auf einen Zylinder aufgerollt, mit Vakuum fixiert und zu einer Folienhülse verschweißt. Danach senkt der Zylinder ab und die Flasche gleitet in die Hülse.
[video nm:20110412-basf-video2a][video nm:20110412-basf-video3a]
Im Schrumpftunnel schmiegt sich die Folie schließlich faltenfrei an die Flasche an. Durch das Verschweißen der Folie auf dem Zylinder und deren Fixierung mit Vakuum lassen sich die technologischen Vorteile der neuen Folienmaterialien voll nutzen und selbst kompliziert geformte Behälter qualitativ hochwertig dekorieren.
[video nm:20110412-basf-video4a][video nm:20110412-basf-video5a]
Diese Verfahren kommen ohne Klebstoff oder Lösemittel zur Fixierung aus, sodass sie besonders für die Lebensmittelverarbeitung und die Reinraumproduktion geeignet sind.
[video nm:20110412-basf-video6a] Eine sehr hochwertige Schweißnaht erzeugt das von Sidel angewandte Wärmeimpulsschweißen (heat and cool bar). Innerhalb von wenigen Millisekunden wird hier die Naht mit Wärme und Druck verschweißt und dann blitzartig abgekühlt.
Der Verfahrensschritt des Aufschrumpfens der Folie gestaltet sich in allen drei Fällen gleich. Die Verweilzeit im Schrumpftunnel beträgt etwa drei Sekunden. Sie muss einerseits lang genug sein, dass die Folie gut aufschrumpfen kann, anderseits aber kurz genug, dass der oft empfindliche Inhalt der bereits befüllten Flaschen durch die erhöhten Temperaturen keinen Schaden nimmt.
Neue Folienmaterialien mit hohem Schrumpf
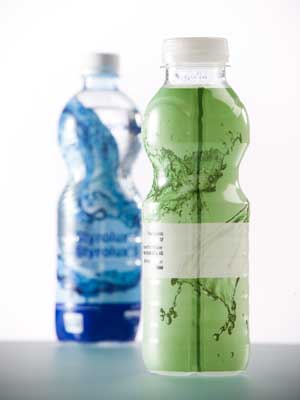
Quelle: Styrolution GmbH
Mit den von der BASF entwickelten Styrolux®-Schrumpffolienprodukten auf Basis Styrol-Butadien-Blockcopolymer (SBC) lassen sich die technologischen Fortschritte der beschriebenen Verfahren optimal nutzen. Mit den hoch transparenten, gut bedruckbaren Folien aus diesem Material sind Schrumpfgrade von bis zu 45 Prozent bei Temperaturen bis 100 Grad Celsius zu erzielen und sogar bis zu 70 Prozent bei Temperaturen jenseits von 100 Grad Celsius. Dabei spielt es keine Rolle, ob als Basis für das MD-Verfahren gereckte Schlauch- oder Flachfolien zum Einsatz kommen.
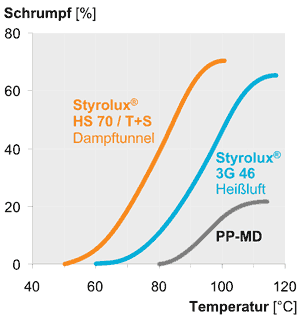
Quelle: Styrolution GmbH
Je nach Anforderung stehen drei unterschiedliche Produkttypen zur Verfügung: Verstreckte Folien aus Styrolux® 3G 46 erreichen ihren maximalen Schrumpf oberhalb von 100 Grad Celsius und sind deshalb besonders für den Heißluft-Schrumpftunnel geeignet. Folien aus Styrolux® HS 70 [1] oder dem erstmals zur K 2011 vorgestellten Zwei-Komponenten-Produkt Styrolux® T/S erfahren ihren höchsten Schrumpf schon bei niedrigeren Temperaturen. Sie empfehlen sich deshalb für das Umschrumpfen im Dampftunnel.
Eine Besonderheit von Styrolux® T/S ist, dass der Folienhersteller die gewünschten Folieneigenschaften innerhalb gewisser Grenzen selbst einstellen kann. Unter anderem ermöglicht das Zwei-Komponenten-Produkt[2] die Herstellung noch dünnerer Folien – eine Option, die nicht nur unter dem Gesichtspunkt der Gewichtseinsparung interessant ist, sondern auch die Wirtschaftlichkeit des Laser- und des Wärmeimpulsschweißens verbessern kann.
Hoch schrumpffähige MD-Folien bereits verfügbar
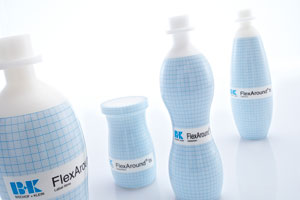
Quelle: BASF / Bischof + Klein
Aus dem Styrolux® der Styrolution GmbH stellt Bischof + Klein (B+K, Lengerich) die Rundumetikettenfolien FlexAround® ts her. Die glasklaren Folien mit brillanter Optik lassen sich auch auf allen für Polyolefine ausgelegten Anlagen verarbeiten. Ihr hoher Endschrumpf bietet Dekorationsmöglichkeiten, wie sie bis dato nur mit TD-Folien realisierbar waren.
Dank der hervorragenden Schrumpfwerte dieser speziellen Folie, dem gleichmäßigen Schrumpf in Maschinenrichtung und der guten Kontrollierbarkeit des Schrumpfvorgangs gibt es nahezu keine Einschränkungen bezüglich der Behälterkontur.
[video nm:20110412-basf-video7a] Die schrumpffähigen Rundumetikettenfolien werden in Breiten von 20 bis 1600 Millimetern bei einer Dicke von 50 Mikrometern (auf Wunsch auch dünner) geliefert und wahlweise im Flexo- und Tiefdruck auf Lösemittelbasis bedruckt. Sie sind einfach zu schneiden, auch auf Hochgeschwindigkeitsanlagen gut zu verarbeiten und sowohl für die Verklebung als auch für die Verschweißung im Impuls- oder Laserverfahren geeignet.
Gemeinsame Präsentation zur Interpack
Die Erfolgsstory der partnerschaftlichen Zusammenarbeit von Anlagenbauer (Sidel), Rohstofflieferant (BASF/Styrolution) und Folienhersteller (B+K) findet auf der Interpack vom 12. bis 18. Mai in Düsseldorf ihre Fortsetzung: BASF/Styrolution (Halle 10, Stand B43) und Sidel (Halle 13, Stand C35) informieren an ihren Ständen über das Folienmaterial und seine Anwendungsmöglichkeiten. Präsentiert wird eine Flasche in neuem, noch komplexerem Design. Wurden bei der auf der K 2010 vorgestellten Flasche Schrumpfwerte bis 50 % realisiert, reichen sie bei der neuen Flasche nun bis 60 %. Am Sidel-Stand wird ihre Dekoration live zu erleben sein.
Interpack 2011:
BASF/Styrolution (Halle 10, Stand B43)
Sidel (Halle 13, Stand C35)
Der Autor, Dipl.-Ing. Michael Schuster, arbeitet im Bereich Business Management SBC-Polymere, Styrolution GmbH, Ludwigshafen
[1] Weiteres zu Folien aus Styrolux® HS 70
[2] New two-component concept for SB copolymers