Verarbeitungssicherheit überzeugt
DPET in der Praxis
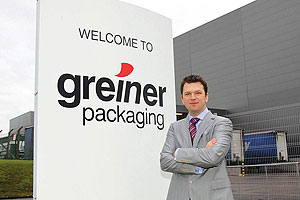
Quelle: Greiner Packaging
Verpackungslösungen für Milchprodukte wie Käse oder Joghurt sind anspruchsvoll, ihre Eigenschaftsprofile müssen gemäß den Marktanforderungen immer weiter geschärft und erweitert werden. Eine für Verpackungshersteller bedeutende Kenngröße lautet daher Konsistenz der Rohstoffe, um die bestmögliche Produktivität (zum Beispiel im Form-Fill-Seal-Prozess) erzielen zu können. Wenn an dieser wichtigen Stellschraube also eine gewisse Ruhe herrscht, fällt es den Verarbeitern leichter, die übrigen, nicht minder herausfordernden Aufgaben zu erfüllen.
Daher will Octal mit dem neuen DPET (direct-to-sheet)-Herstellungsverfahren für PET-Hartfolien auf dem globalen Markt überzeugen - mit großem Selbstvertrauen ausgestattet hat das Unternehmen spätestens zur interpack vor wenigen Wochen auf die positiven Eigenschaften des neuen Materials hingewiesen. Einige Verarbeiter machen bereits Praxiserfahrungen mit DPET, einer davon ist Greiner Packaging in Nordirland, das Unternehmen lässt die Mitwelt an den ersten Erfahrungen mit DPET für thermogeformte Behälter für die Milchindustrie teilhaben.
Jarek Zasadzinski, CEO von Greiner Packaging UK, zeigt sich nach mehrmonatigen Tests mit dem neuen Material außerordentlich zufrieden und erklärt, die Erfahrungen mit DPET übersteige die in die Innovation gesetzten Erwartungen. Octal habe damit neue Wege beschritten. Seit Mitte 2010 arbeitet Greiner UK mit dem Material und verarbeitet es zu thermogeformten Schalen für die Milchwirtschaft und für Dessertvariationen. Typische Lösungen sind Verpackungen für die britischen Handelsketten wie Tesco, Asda, Sainsbury's etc., wie J. Zasadzinski auf Nachfrage von verpacken-aktuell.de erklärt.
Kunden zeigen sich begeistert
Und er fasst seine Eindrücke zusammen: "Der Materialprozess ist ausgezeichnet. Dank seiner Eigenschaften sind die Einrichte- und Rollenwechselzeiten minimiert. Die Schalen zeigen ein hervorragendes Finish, das unsere Kunden lieben. Wir haben festgestellt, dass wir mit DPET ein wesentlich besser beherrschbares Materialhandling erhalten, als je zuvor mit PET. Da das Material so konstante Qualität aufweist, ist die Prozesskontrolle deutlich leichter als zuvor."
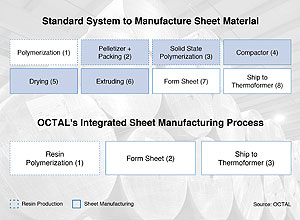
Quelle: Octal
DPET von Octal ist die erste und einzige direct-to-sheet-Polyesterfolie der Welt. Damit ist es erstmals gelungen, fünf Phasen des herkömmlichen Folienherstellungsverfahrens ersatzlos zu eliminieren. Konkret handelt es sich dabei um die Streichung von Granulierung, Festphasenpolykondensation (SSP), Verdichtung, Trocknung und Pressen (siehe Abbildung 1). Durch diese Technologie, Ergebnis langjähriger Forschungsarbeiten, werden PET-Folien mit verbesserten optischen und mechanischen Eigenschaften produziert. Es wird nicht nur eine höhere Produktivität beim Thermoformen gewährleistet, sondern nachweislich Vorteile für die Umwelt, Stichwort Nachhaltigkeit, erbracht. Durch spezielle Software-Programme und eine eigene Verfahrenssteuerung wird die Produkteinheitlichkeit von Rolle zu Rolle maximiert.
Die Eigenschaften von DPET ermöglichen einen höheren Materialfluss zu den Ecken des Behälters, typischerweise die schwächsten Stellen, sodass eine reduzierte Foliendicke und dadurch Materialeinsparungen und Abfallvermeidung erreicht werden. Um den Stößen und Erschütterungen während des Transports standzuhalten, zeichnet die neue Folie eine hohe Stabilität bei Stapelungen und Mehrstückverpackungen aus.
Dazu noch einmal Jarek Zasadzinski: Unsere Kunden haben die ökologischen wie auch technischen Vorzüge von DPET eindeutig akzeptiert."
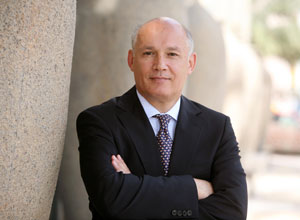
Quelle: Octal
Octal ist ein vergleichsweise junges Unternehmen, gegründet 2006 von privaten und institutionellen Investoren im Sultanat Oman. Gestartet wurde in Salalah im Süden des Omans, mit einer Jahreskapazität von rund 30.000 Tonnen traditionellem PET. Bald wurde das Werk vergrößert, womit die Jahresproduktion auf 300.000 Tonnen stieg. Durch bessere Maschinen und innovative Produktionsverfahren kletterte die Kapazität im Jahr darauf auf 400.000 Tonnen. Die zweite Expansionsphase ist zur Zeit im Gang, womit die Produktion auf insgesamt über 900.000 Tonnen im Jahr 2012 steigen wird.
Doch damit nicht genug, wie die Umsatzzahlen eindrucksvoll beweisen: Konnte 2010 ein weltweiter Umsatz von rund 430 Mio USD erzielt werden, so ist für 2011 ein Umsatz von rund 600 Mio USD geplant. Nächstes Jahr, mit dem neuen Werk in Salalah und der prognostizierbaren Nachfrage nach DPET, wird ein Umsatz von 1,5 Mrd USD angepeilt. Nicholas P. Barakat, CEO von OCTAL: "Wir wachsen stark, ja. Doch unser wichtigeres Ziel ist die Technologieführerschaft. Mit DPET wollen wir den Märkten die grüne Hartfolienverpackung anbieten. Dafür werden wir in den nächsten fünf Jahren nochmals rund 900 Mio USD investieren."
Mit seinen rund 400 Mitarbeitern liefert Octal seine DPET-Polyesterfolien weltweit in über 60 Länder nach Europa, Amerika und Asien.
Kleinster CO2-Fußabdruck
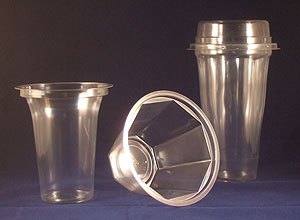
Quelle: Greiner Packaging
Der entscheidende Vorteil von DPET liegt nach Einschätzung des Herstellers im CO2-Fußabdruck. Keines der weltweit vergleichbaren PET-Materialien hat einen vergleichbar niedrigen CO2-Fußabdruck wie DPET. So bestätigten die unabhängigen Experten von Intertek, dass DPET einen um 25 Prozent niedrigeren CO2-Fußabdruck als herkömmliches APET hat. Es folgt eine noch detailliertere Beschreibung für Experten: Bei Betrachtung des funktionellen Äquivalents einer Tonne APET hat DPET eine Auswirkung von 3.088 Tonnen CO2eq. Dieser Betrag liegt 1031 Tonnen unter dem von APET.
Das "Sustainibility Consortium" aus den USA (Universität Arkansas) spendet Octal und DPET Beifall zur Produktionsmethode: "Octal zeigt damit im Bereich Nachhaltigkeit die richtigen Wege auf." Durch den weltweit einzigartigen Einsatz eines selbst entwickelten Zwei-Reaktoren-Systems können fünf Produktionsschritte eingespart werden.
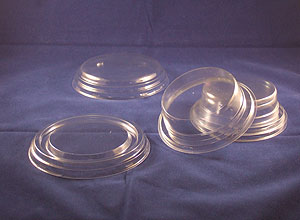
Quelle: Greiner Packaging
Auch beim Energiebedarf beschreitet Octal neue Wege. Zum einen stammt der gesamte Bedarf aus sauber brennendem Erdgas, zum anderen wird durch einen eigens adaptierten Brenner bis zu 20 Prozent weniger Gas verbraucht. Die Einsparungen beim Strom betragen ca. 67 Prozent im Vergleich zur herkömmlichen Folienproduktion.
Größtes Augenmerk wird schlussendlich auch auf einen verantwortungsvollen Umgang mit Wasser gelegt. Für die Produktion von DPET werden deshalb zu 100 Prozent kommunale Abwässer verwendet. Mittels Umkehrosmose und Sandfiltrationssysteme wird dieses Wasser wieder aufbereitet und großteils neuerlich in das Herstellungssystem eingespeist. Der Rest des Wassers wird zur Bewässerung eines neu geschaffenen Grüngürtels rund um den Produktionsstandort eingesetzt. Der ökologische Kreislauf ist damit geschlossen.
Mike Faupel, Direktor des Sustainibility Consortiums an der Universität von Arkansa hat die Materialien von Octal mit Blick auf ihre Umweltverträglichkeit auf Herz und Nieren geprüft. Sein Resümee: "Octal nimmt im Bereich Umweltschutz und Nachhaltigkeit eine internationale Vorreiterrolle ein. Die Zahlen sind wissenschaftlich fundiert, die Transparenz ist außerordentlich hoch."
Lesen Sie hierzu auch die folgenden Beiträge:
Globale PET-Nachfrage zuverlässig befriedigen
Neuer Rohstoff DPET™ feiert Premiere
(st)