Waldorf Technik
Volle Flexibilität im Inmould-Labelling - auch mit Barriere
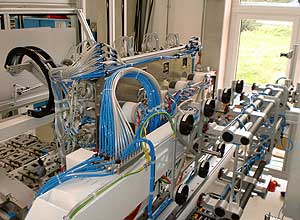
Quelle: Waldorf Technik
Anlässlich der Fakuma in Friedrichshafen zeigt Waldorf Technik, Engen, auf, mit welchem technologischen Ansatz Fortschritte beim Inmould-Labelling erzielbar sind. Kurze Zykluszeit und hohe Kavitätenzahl war bisher das Maß der Dinge bei IML-Automationen. Als entscheidender Erfolgsfaktor kristallisiert sich bei Experten zunehmend die Flexibilität der Anlagen heraus. Waldorf Technik als Pionier in diesem Feld will mit seinem modularen Konzept völlig neue Maßstäbe setzen. Maximale Leistung als Produkt aus kurzer Zykluszeit und hoher Kavitätenzahl ist häufig das wichtigste Kriterium bei der Auswahl von Produktionsanlagen. Beim Inmould Labelling ist das oft nicht anders. In Zusammenarbeit mit seinen Kunden hat Waldorf Technik in den letzten Jahren erkannt, dass ein weiteres Kriterium für diese Kunden erfolgsentscheidend ist: die schnelle Umrüstbarkeit der IML-Automationen auf unterschiedliche Produkte und unterschiedliche Kavitätenzahlen.
Ursache dafür sind die individuellen Kundenbedarfe und die teils relativ kleinen, vor allem aber saisonabhängigen Abrufmengen der Abfüller. So werden Partysalate vorrangig in der Grillsaison und in Schönwetter-Perioden verkauft. Ebenso werden Non-Food-Produkte wie Außenfarbe vorrangig in der warmen Jahreszeit benötigt. In den übrigen Zeiten ist der Bedarf niedriger. Um aber als Verpackungshersteller das ganze Jahr über erfolgreich zu sein, müssen auch diese Zeiten mit Aufträgen gefüllt werden.
"Eine hohe Anlagenleistung allein ist hier nicht mehr ausreichend für den Erfolg des Spritzgießers. Wichtig ist in solch einer Marktumgebung, dass die Anlagen das ganze Jahr über ausgelastet sind", erläutert Wolfgang Czizegg, Geschäftsführer der Waldorf Technik GmbH & Co. KG. Und auf diese Vollauslastung der IML-Anlagen konzentriert sich das Unternehmen mit seiner seit Jahren erfolgreichen modularen Produktserie highflex® IML. IML-Automationen dieses Typs sind flexibel einsetzbar für alle gängigen Etikettengeometrien sowie auch für Werkzeuge von 1-8 Kavitäten. Umrüstzeiten von weniger als 30 Minuten, womit das Unternehmen weltweit konkurrenzlos schnell ist, runden das Flexibilitätspaket ab.
Erst im letzten Jahr wurden mit dem weiteren Ausbau des Baukastensystems neue Meilensteine gesetzt. So können jetzt innen und außen angespritzte Produkte auf einem einzigen IML-Roboter hergestellt werden. Erst jüngst wurden highflex® IML -Anlagen erfolgreich mit Formatteilen zur Herstellung von 2-Kammer-Bechern mit 8 Kavitäten und insgesamt 24 Labeln ausgeliefert. Ferner können Kunden von Waldorf Technik heute Becher, Container oder auch Deckel mit bis zu 32 Kavitäten auf highflex® IML -Anlagen produzieren, womit das Unternehmen weltweit den Vorsprung zu anderen Robotbauern weiter ausgebaut hat.
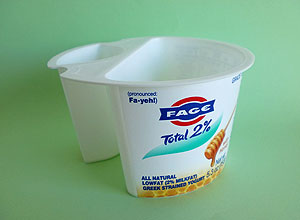
Quelle: Waldorf Technik
Die Bedeutung von Produktschutz als Teilfunktion der Verpackung nimmt laufend zu. Sowohl wirtschaftliche Vorteile der Abfüller als auch gesundheitliche Aspekte für den Konsumenten treiben diese Entwicklungen massiv voran. Waldorf Technik konnte diesem Trend in den vergangenen Monaten durch neue Technologien deutliche Impulse geben.
Vor über 8 Jahren entwickelte die Waldorf Technik GmbH & Co. KG zusammen mit einem bekannten Markenartikler die erste Barriere-Spritzguss-Verpackung und lieferte die dazu notwendige Automation zur industriellen Fertigung dieser Behälter. "Ohne es genau zu wissen war dies vermutlich die weltweit erste Barriere-IML-Spritzgussverpackung für Nahrungsmittel mit einer Mindesthaltbarkeitsdauer von mehreren Jahren. Diese Entwicklung gab der gesamten Branche Impulse und legte für Waldorf Technik den Grundstein zur Weiterentwicklung unserer Barriere-Technologien", resümiert Geschäftsführer Wolfgang Czizegg heute.
Maßgebliche Gründe für den Einsatz von Behältern mit Barriere-Eigenschaften liegen sowohl in wirtschaftlichen wie auch in gesundheitlichen Gründen. Die Verlängerung des sogenannten Shelf-Lifes, der Mindesthaltbarkeitsdauer von Lebensmitteln, durch eine Sauerstoffbarriere vereinfacht die Logistik wie auch die Produktionsplanung für Lebensmittelhersteller, was deren Kosten massiv senkt. Auch können durch Einsatz von Spritzguss-Verpackungen statt teurer Konservendosen oder -gläser Kostensenkungen von bis zu 40 % erzielt werden. Darüber hinaus gibt es Methoden die unerwünschte Migration von Fremdstoffen wie Masterbatches, Weichmacher oder andere Elemente aus der Verpackung in die Füllgüter zu unterbinden, was unter gesundheitlichen Aspekten mehr und mehr gefordert wird. Selbst der Einsatzbereich von biologisch abbaubaren Werkstoffen kann durch Barriere-Funktionen erweitert werden.
Mittlerweile unterstützt Waldorf Technik mit seinen Hightech-Automationen maßgeblich drei Verfahren zur Herstellung von Barriere-Verpackungen im Spritzgieß-Verfahren: das Nano-Glass-Coating, das EVOH-Spritzgießen, und das Inmould Labelling mit Barriere Labels.
Das Inmould Labelling als Dekorationsverfahren ist eine bereits sehr weit verbreitete Technologie, in der Waldorf Technik heute einen signifikanten Marktanteil besitzt. Die Fortentwicklung dieses Verfahrens durch die Verwendung von Labels mit Barriereeigenschaften wie etwa O2-Barriere oder UV-Barriere ist nur ein relativ kleiner weiterer Schritt.
Das erste für große Mengenbedarfe geeignete Verfahren zur Herstellung von Barriere-Spritzguss-Behältern, das EVOH-Co-Injection-Verfahren, ist 2010 marktreif geworden. Neben dem Polypropylen wird auch EVOH als Mittelschicht eingespritzt. EVOH hat gute Barriereeigenschaften und verleiht dem Behälter damit die nötige Funktion, um beispielsweise Fischkonserven, Petfood-Container, Konservendosen oder Gläser für jegliches Füllgut zu ersetzen. Der Kostenvorteil dürfte bei gut 30-40 % liegen. Hinzu kommen logistische Vorteile durch Stapelfähigkeit von spritzgegossenen Behältern gegenüber von klassischen Dosen oder Gläsern. Entscheidend für den Marktdurchbruch war eine 100%-Kontrolle der Kunststoff-Behälter, für die Waldorf Technik zusammen mit Kunden und Partnern eine einzigartige Technologie entwickelt hat. Knapp 20.000 Behälter pro Stunde werden aus der Spritzgussmaschine entnommen, zu 100% auf die vollständige EVOH-Schicht geprüft, anschließend vollautomatisch abgepackt und palettiert.
Das dritte Verfahren zur Herstellung von Barrierebehältern im Spritzgussverfahren ist das Nano-Glass-Coating. Hier wird eine hauchdünne, hochflexible glasähnliche Schicht auf die Innen- oder Außenseite eines Bechers appliziert, wodurch einfachste Kunststoffbecher beste Barriereeigenschaften erhalten - und das nahezu zum Nulltarif, da der Materialverbrauch extrem gering ist. Neben der hohen O2-Barriere unterbindet diese Technologie auch jegliche Migration, sei es von Stoffen von außen oder aus dem Bechermaterial in das Füllgut, oder auch ätherische Öle oder Aromen vom Füllgut nach außen. Auch kann kostengünstiges Monomaterial als Kunststoff verwendet werden, ebenso kann dieses problemlos als Monomaterial recycelt werden. Waldorf Technik steuert in dieser Technologie die Synchronisation der unterschiedlichen Zykluszeiten sowie prozessbedingte Sonderfunktionen mittels Automation bei.
Waldorf Technik auf der Fakuma: Halle B2 auf dem WVIB-Gemeinschaftsstand, Stand-Nr. 2204. Im Themenpark Medizintechnik auf der Aktionsfläche im Foyer West
(st)