Maschinenbauer sehen sich als prädestiniert für das Zukunftsthema
In-house EXPO bei W&H unter dem Motto PACKAGING 4.0
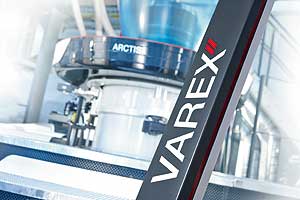
Quelle: Windmöller & Hölscher
Der Begriff „Industrie 4.0“ ist in aller Mund. Es war das beherrschende Thema der letzten Hannover-Messe und nicht nur dort. Die Wirtschaft stehe an der Schwelle zur 4. Industriellen Revolution heißt es in den Fachmedien, und es wird die Frage diskutiert, ob die deutsche Industrie, insbesondere die mittelständischen Unternehmen, auf diese Herausforderung überhaupt vorbereitet sei. Mit dem Motto PACKAGING 4.0 bringt Windmöller & Hölscher zum Ausdruck, dass das Unternehmen sich dieser Herausforderung stellt. Die EXPO zeige, welche neuen Möglichkeiten die 4. Industrielle Revolution durch Vernetzung der Produktionsanlagen und datentechnische Durchdringung der Fertigung für die Packmittelproduktion eröffnen wird und gleichzeitig zur Diskussion über dieses spannende Zukunftsthema auffordern, so die Geschäftsführung von W&H.
Aufgrund der weltweit einzigartigen Durchgängigkeit der Produkte aus den Bereichen Extrusion, Druck und Verarbeitung sieht sich W&H wie kein anderes Unternehmen prädestiniert für das Thema PACKAGING 4.0.
„PACKAGING 4.0 bedeutet für W&H: Integrierte Prozessketten in der Produktion flexibler Verpackungen, die datentechnisch vernetzt, mit leistungsfähiger Sensorik und hoch spezialisierten Automationsmodulen ausgestattet sind und die sich durch intuitive Bedienung sowie intelligente Reaktion auf Änderungen der Prozessparameter auszeichnen“, so die Definition von Dr. Jürgen Vutz, Vorsitzender der W&H-Geschäftsführung.
W&H stellt sich den Megatrends der Branche und gibt Antworten auf die drängenden Fragen steigender Rohstoffpreise, knapper Ressourcen, zunehmenden Preisdrucks und sinkenden Qualifikationsniveaus. Die EXPO diente dazu, den Kunden Lösungen aufzuzeigen, wo W&H-Module helfen können, besser und wirtschaftlicher zu produzieren. Gleichzeitig wurde die EXPO als Einstieg in die Diskussion mit den Kunden zum Thema PACKAGING 4.0 genutzt.
Varex II: Produktivitätssteigerungen und Produktinnovationen im Fokus
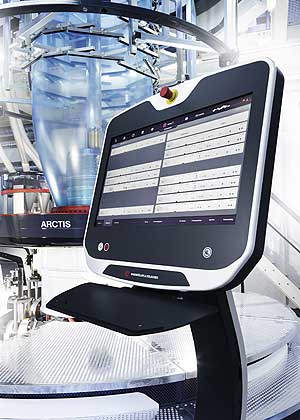
Quelle: Windmöller & Hölscher
Der Beginn einer neuen Ära, so wurde die Vorstellung der VAREX II auf der K 2013 seinerzeit tituliert. Mit dieser Neuentwicklung habe Windmöller & Hölscher die nächste Generation der Blasfolienextrusion auf den Markt gebracht, so lautete die Reaktion vieler, als sie die neue Blasfolienanlage das erste Mal sahen. Die diesjährige EXPO nutzte W&H, um dem Fachpublikum mit insgesamt drei Varex II-Anlagen ganz unterschiedlicher Konfiguration Beispiele für Produktivitätssteigerungen und Produktinnovationen zu präsentieren.
Schnelle Materialwechsel und kurze Spülzeiten dank intelligenter Automation
An der ersten Anlage stand das Thema Rohstoffwechsel mit Hilfe von Automationsmodulen und Spülprogrammen bei der Produktion von Kaschierfolie im Fokus. Benötigte ein Maschinenführer bislang für die händische Umstellung einer 3-Schicht-Anlage ca. eine halbe Stunde, so ist es W&H jetzt gelungen, diesen Wechselprozess dank der Automatisierung auf nur noch zwei Minuten zu senken. Möglich wird dies durch die Kombination eines intelligenten Steuerungs-Algorithmus mit der automatischen, pneumatischen Reinigung von Gravimetrik und Saugförderern. Der Maschinenführer muss lediglich noch die Sauglanze von einem Rohstoffbehälter in den anderen umstecken.
EXPO-Besucher konnten sich während der Vorführung persönlich von diesem Quantensprung bei der Reduzierung von Umstellzeiten überzeugen. Gezeigt wurde der Umstellprozess auf einer 3-Schicht-Anlage Varex II mit 280 mm Düse und einer Arbeitsbreite von 2200 mm.
Down Gauging atmungsaktiver Backsheet-Folie durch den Prozess des inline-Verstreckens mit Hilfe eines Reckwerks (MDO)
Gezeigt wurde eine 3-Schicht-Blasfolienanlage Varex II mit inline- MDO-Reckwerk und integrierter Dickenprofilregelung Optifilp-MDO. Mit Hilfe der MDO-Technologie lassen sich Kunststofffolien mit einzigartigen Eigenschaftsspektren realisieren bei gleichzeitiger Reduzierung der Foliendicke. Im konkreten Fall geht es um die Herstellung einer besonders dünnen, atmungsaktiven Windel-Backsheet-Folie von nur noch 12 g/m² im Blasfolienverfahren mit inline-Längsverstreckung.
Folien für dieses Anwendungsgebiet werden heutzutage vorzugsweise im Gießfolienverfahren produziert, mit einem Flächengewicht von 14 – 17 g/m². „Der Trend geht aber ganz eindeutig in Richtung Blasfolie“, zeigt sich Lennart Ederleh, Leiter Kundenberatung Extrusionsanlagen überzeugt. „Blasfolien werden die Gießfolien hier ablösen, da einerseits andere Rohstoffe zum Einsatz kommen und andererseits prozessbedingt eine Biaxiale Orientierung der Moleküle erzeugt wird. Beide Aspekte verbessern die mechanischen Eigenschaften der Folie und damit das Down Gauging-Potenzial.“
Beim MDO-Verfahren werden im Blasfolien- oder Gießfolienprozess hergestellte Folien in Maschinenlaufrichtung kontinuierlich verstreckt. Durch diesen Verstreckvorgang wird sowohl die Foliendicke reduziert als auch die Morphologie der Folie gezielt verändert. Die Atmungsaktivität wird durch ein Verstrecken mineralisch gefüllter Folien realisiert. Beim Verstreckvorgang löst sich die Polymermatrix von den Füllstoffpartikeln, wodurch ein feines Netzwerk von Mikroporen entsteht. Diese Mikroporen ermöglichen den Durchtritt von Gasen durch die Folie, stellen aber weiterhin eine Undurchlässigkeit gegenüber Flüssigkeiten sicher.
Beim Verstrecken der Folie in Maschinenrichtung reduziert sich allerdings nicht nur die Foliendicke. Es kommt auch zu einer Reduzierung der Folienbreite durch Einschnüren. Dieser so genannte Neck-In-Effekt führt schließlich zu einem Foliendickenprofil in Querrichtung mit ausgeprägten Dickstellen in den Randbereichen. Um jedoch eine problemlose Weiterverarbeitung der gereckten Folie in den nachfolgenden Produktionsschritten zu gewährleisten, muss dieser Neck-In-Bereich vor dem Aufwickeln durch einen beidseitigen Randbeschnitt entfernt werden. Da die abzuführenden Randstreifen jeweils eine Breite von bis zu 150 mm aufweisen können, wird somit die Nettoausstoßleistung der Anlage reduziert. Um diesen Randbeschnitt zu reduzieren und damit Material einzusparen, kommt an der vorgeführten Anlage die integrierte Dickenprofilregelung Optifilp-MDO zum Einsatz, die für eine konstante Dicke der gereckten Folie sorgt, so dass bis zu 50% des Randbeschnitts eingespart werden können. Dieses Exponat machte die Idee von PACKAGING 4.0 besonders deutlich, denn die auf der Varex II produzierte atmungsaktive Windelfolie wird anschließend auf einer Flexodruckmaschine Vistaflex bedruckt.
Wiederverschließbare Hoch-Barrierefolie als Deckelmaterial für Lebensmittelverpackungen
Ein Blick in die Kühlregale der Supermärkte macht es deutlich: Wiederverschließbare Verpackungen z.B. für Wurst oder Käse sind charakteristisch für den veränderten Lebensstil der Verbraucher und daher aus der heutigen Zeit nicht mehr wegzudenken. Bei der Herstellung dieser Verpackungen stellt insbesondere der Wunsch nach Wiederverschließbarkeit sehr große Anforderungen an die Folie, die als Deckelmaterial eingesetzt wird. Hier kommen seit langem sogenannte „Pressure Sensitive Adhesives“ (PSA) zum Einsatz, die aufgrund ihrer extrem hohen Klebkraft sehr schwer zu verarbeiten sind. „Windmöller & Hölscher ist es nun gelungen“, berichtet Dr. Falco Paepenmüller, Leiter Produktbereich Extrusion, nicht ohne Stolz, „eine Möglichkeit zu finden, wie dieses Material in Verbindung mit einer Hochbarriere aus PA-EVOH-PA unkompliziert zu einer hochwertigen, 9-Schicht-Barrierefolie mit PSA-Hotmelt-Schicht für „reclosable“-Deckelanwendungen verarbeitet werden kann.“ Gezeigt wurde diese zukunftsweisende Entwicklung auf einer 9-Schicht-Anlage Varex II in 2600 mm Arbeitsbreite und mit einer 500 mm Düse.
Weltpremiere: Aquarex mit neuem Kalibrator Aquacage
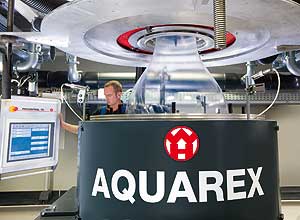
Quelle: Windmöller & Hölscher
Seit ihrer Markteinführung hat sich die Aquarex, die modulare Blasfolienanlage mit Wasserkühlung der Folienblase, einen hervorragenden Ruf bei der Produktion von innovativen Folienprodukten erworben. Die Flexibilität der Anlage hinsichtlich der Folienbreite war allerdings durch den Einsatz von Festkalibratoren eingeschränkt. Bei einer Änderung der Folienbreite musste der Kalibrator getauscht werden. Mit der Entwicklung des verstellbaren Wasserkalibrators Aquacage, den Windmöller & Hölscher jetzt auf der EXPO erstmals der Öffentlichkeit präsentierte, ist es dem deutschen Maschinenhersteller gelungen, diese Einschränkung zu beseitigen, die Flexibilität der Gesamtanlage zu erhöhen und damit auch die Anwendungsvielfalt nochmals zu steigern. Auf der EXPO wurde die Aquarex mit der Herstellung einer asymmetrischen Hochbarrierefolie für Thermoformanwendungen gezeigt.
Durch den Prozess der Wasserkühlung weisen die Folien eine sehr gute Transparenz und einen hohen Glanz auf. Durch die amorphen Bereiche ergibt sich eine sehr gute Schweißbarkeit und Durchstoßfestigkeit. Zudem zeichnet sich die Folie durch eine sehr gute Thermoformbarkeit im Vergleich zu Blas- und Gießfolie aus, wie während der Hausmesse zu sehen sein wird.
Die EXPO bietet auch die Plattform für die Weltpremiere des neuen verstellbaren Wasserkalibrators Aquacage, dessen Entwicklung soeben abgeschlossen wurde. Der Kalibrator erlaubt die automatische Verstellung des Durchmessers der Blase ähnlich wie bei der konventionellen Blasfolienextrusion. Daher ist ab sofort kein Wechsel von Festkalibratoren mehr erforderlich, was in einer erhöhten Flexibilität der Aquarex resultiert. Ein verstellbarer Kalibrator passt vom Durchmesserbereich zu einer Blaskopfgröße. „Wir sind sehr froh, dieses innovative Modul jetzt vorstellen zu können“, unterstreicht Lennart Ederleh und beschreibt die nächsten Schritte: „Unmittelbar nach der Hausmesse wird der neue Kalibrator an einen ersten Kunden gehen.“
Verpackungsdruck langfristig auf Wachstumskurs
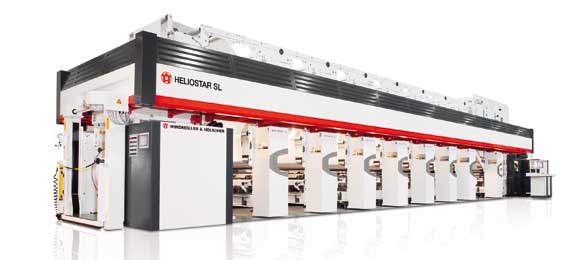
Quelle: Windmöller & Hölscher
Das W&H-Maschinenprogramm für den Verpackungsdruck sieht das Unternehmen nach wie vor in robuster Verfassung. Dies gilt insbesondere für den Druck flexibler Verpackungen. Dieses Marktsegment wird aufgrund der Flexibilität und Ressourceneffizienz flexibler Verpackungen auch in Zukunft wachsen. Im Rahmen der Hausausstellung EXPO präsentierte Windmöller & Hölscher Innovationen aus allen Bereichen seines Maschinenprogramms zur Herstellung und Verarbeitung flexibler Verpackungsmaterialien, so auch aus dem umfassenden Druckmaschinen-Portfolio. Gezeigt wurden Flexo- und Tiefdruckmaschinen in unterschiedlichen Konzept-, Leistungs- und Ausstattungsversionen. Mit der Miraflex S feierte das jüngste Mitglied der Miraflex-Familie seine Premiere vor großem Publikum.
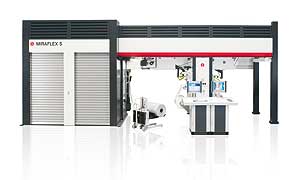
Quelle: Windmöller & Hölscher
Exemplarisch für die Facetten von PACKAGING 4.0 stand auf der EXPO eine Konfiguration von Varex II und Vistaflex CL 8: Die Vistaflex CL 8 ist das leistungsstärkste Modell im W&H-Flexodruckmaschinenprogramm für große Druckbreiten. Sie setzt die Verarbeitung einer Windelfolie fort, die vorher auf einer VAREX II produziert wurde. Bedruckt wird eine atmungsaktive 12 g/m² dünne Windelfolie (back sheet) bei einer Druckgeschwindigkeit von 800 m/min und 7-nutzigem Inline-Schnitt.
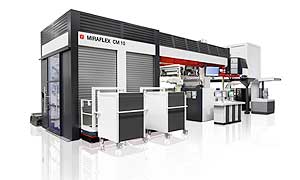
Quelle: Windmöller & Hölscher
Mit der Miraflex CM 10 setzt W&H ein Zeichen für Nachhaltigkeit im Flexodruck. Die Maschine ist mit einer regelbaren, energieeffizienten Hochleistungstrocknung ausgestattet, die selbst bei hoher Farbübertragung Druckgeschwindigkeiten bis 600 m/min erlaubt. Zum Zweck der Verbrauchsoptimierung werden dabei die eingesetzten Elektro-, Gas-, Kühlwasser- und Druckluftenergien mit Hilfe der Neuentwicklung „Energy Monitoring“ im Druckprozess kontinuierlich erfasst. An Hand von Vergleichswerten kann die Maschine in einem energieoptimierten Betriebszustand gefahren werden, während gleichzeitig auftragsbezogene Energieverbräuche dokumentiert werden können.
Ein Beitrag zur Nachhaltigkeit ist auch die Vermeidung von Ausschuss. Erstmals wurde dazu die Inline-Rapportmessung mittels Easy-Set HD der Öffentlichkeit vorgestellt. Das System sorgt dafür, dass auch bei stark dehnenden Substraten die exakte Rapportlänge permanent eingehalten wird. Auswirkungen von Bahnspannungs-, Trocknungstemperatur- oder anderen Prozessänderungen auf die Rapportlänge werden erkannt und korrigiert.
An der Tiefdruckmaschine Heliostar S wurde mit der neuartigen Heliocontrol-Sensortechnik die Registergenauigkeit im Tiefdruck neu definiert. Vorgeführt wurde die Maschine mit dünnen Verpackungsfolien und einer Geschwindigkeit von 500 m/min.
W&H-Maschinen für ihre Energieeffizienz ausgezeichnet
Der TÜV Süd zertifiziert Blasfolienanlagen und Flexodruckmaschinen: Das Energieeffizienzlabel erhalten alle W&H-Blasfolienanlagen der Baureihen Optimex und Varex in den Ausführungen von 3 bis 9 Schichten. Wegen der schwierigen Vergleichbarkeit von Daten, die an unterschiedlichen Anlagen erfasst werden können, fanden Untersuchungen bisher fast immer nur an einzelnen Komponenten einer Extrusionsanlage statt. Erstmals wurde nun vom TÜV Süd eine komplette Baureihe von Blasfolien-Extrusionsanlagen hinsichtlich ihres Energieverbrauchs auditiert und nach eingehender Auswertung mit dem Zertifikat „beste verfügbare Technik“ in Bezug auf die Energieeffizienz ausgezeichnet. Auch für die Flexodruckmaschinen Vistaflex und Miraflex liegen TÜV-Zertifikate vor. Damit wird seitens des TÜV Süd bescheinigt, dass die W&H-Maschinen der genannten Baureihen den Anforderungen hinsichtlich Energieeffizienz in vollem Umfang entsprechen.
(st)