Internet of Things Gateway für vernetzte Fertigung
Längeres Leben für den Maschinenpark
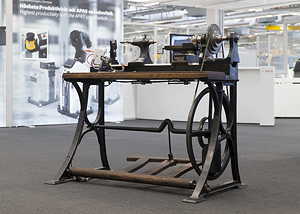
Robert Boschs Drehbank aus dem Jahr 1887
Quelle: Bosch
Mit einem Alter von fast 130 Jahren, pedalbetrieben und ein museales Stück Industriegeschichte, an dem Unternehmensgründer Robert Bosch ab 1887 noch persönlich gearbeitet hat, ist die 300 Kilogramm schwere, gusseiserne Drehbank Anschauungsobjekt für Retrofit-Potenziale heutiger Maschinen.
Denn der Bosch-Konzern zeigt an der Drehbank, wie mit Hilfe von Sensorik, Software und einer IoT-fähigen Industriesteuerung Nachrüstungsmöglichkeiten umgesetzt werden können. So werden auch deutlich jüngere, aber eben noch nicht vernetzt arbeitende Maschinen und Anlagen fit für Industrie 4.0 gemacht.
507 Mark für die Drehbank
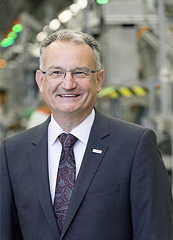
Dr.-Ing. Werner Struth, Geschäftsführer bei Bosch
Quelle: Bosch
Robert Bosch hatte die Drehbank im Februar 1887 gekauft und auch selbst daran gearbeitet. Sie war vermutlich bis 1901 im Einsatz. Umgerechnet auf heutige Verhältnisse entspricht der damalige Kaufpreis von 507 Mark etwa 30 000 bis 40 000 Euro – für den kleinen Betrieb, den Robert Bosch erst 1886 gegründet hatte, war das eine beträchtliche und auf Dauer gerechnete Investition. „Daran hat sich bis heute nichts geändert: Maschinen sind teuer. Wir müssen sie so effizient wie möglich nutzen. Das Vernetzen hilft uns entscheidend dabei“, sagte Dr. Werner Struth in der Bosch-Geschäftsführung unter anderem für die Industrietechnik und die Fertigungskoordination verantwortlich, in Stuttgart.
Unter anderem wurden auf der Drehbank ursprünglich Teile für den Magnetzünder gefertigt, jenes Produkt, das Bosch Ende des 19. Jahrhunderts zum Durchbruch verhalf. Nun wurde die historische Maschine auf einen Schlag aus dem Museum ins Industrie 4.0-Zeitalter katapultiert. Sein technischer Unterstützer: das neue IoT (Internet of Things) Gateway von Bosch.
Das vernetzte System kombiniert Sensorik, Software sowie eine IoT-fähige Industriesteuerung und ermöglicht damit die Zustandsüberwachung der Drehbank. „Unser weltweit einmaliger Aufbau zeigt, dass selbst älteste Maschinen mit dem IoT Gateway schnell und einfach vernetzt werden können“, sagte Struth, „Damit erschließt Bosch auch Betreibern älterer Maschinenparks die Vorteile der vernetzten Industrie“.
Viele Maschinen noch nicht Teil der Industrie 4.0
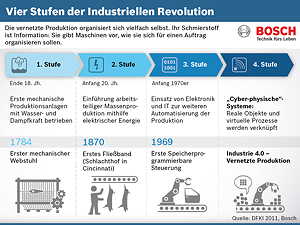
Vier Stufen der Industriellen Revolution
Quelle: Bosch
„Viele Maschinen im Handwerk oder in der Fertigung sind noch ohne Industrie 4.0-Anbindung. Unter anderem fehlen ihnen Sensoren, Software oder die Anbindung an IT-Systeme des Unternehmens – und damit wesentliche Voraussetzungen für die vernetzte Fertigung. Allein in Deutschland sind mehrere zehn Millionen Maschinen betroffen. Global betrachtet ist das ein Milliardenmarkt für Retrofit-Lösungen wie das Bosch IoT Gateway“, sagte Struth.
Die Industrie brauche vernetzte Maschinen, wenn sie nachhaltig Erfolg haben solle. Genau das leistet das IoT Gateway, schnell und flexibel. Bosch zeigt damit, wie Betreiber älterer Produktionsanlagen ihre Maschinen vernetzen, dadurch in Echtzeit überwachen und somit optimieren können. Das ermöglicht etwa die vorausschauende Wartung und reduziert somit Ausfallzeiten bei gleichzeitig steigender Produktivität.
Lange Innovationszyklen machen Retrofit-Lösungen nötig
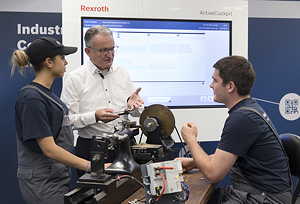
Bosch-Geschäftsführer Dr. Werner Struth mit den Auszubildenden Sina Rohloff und Felix Meeh an der Drehbank.
Quelle: Bosch
Der technische und wirtschaftliche Hintergrund für das IoT Gateway: Innovationszyklen im Maschinenbau unterscheiden sich von jenen in vielen anderen Branchen. Einmal angeschaffte Maschinen bleiben oft über Jahrzehnte im Einsatz. Sie lassen sich nur mit hohem Aufwand und mit hohen Kosten an neue Anforderungen anpassen. Ein großer Teil des weltweit installierten Maschinenparks ist daher noch ohne Anbindung an die vernetzte Fertigung. Der Bedarf für sogenannte Retrofit-Lösungen zum Nachrüsten für die vernetzte Fertigung ist daher nach Einschätzung von Bosch riesengroß.
Das gilt auch für das Unternehmen selbst: „Wir setzen das IoT Gateway bereits in eigenen Anlagen ein und sparen damit Geld. Zum anderen bietet unsere Tochter Bosch Rexroth diese Lösung ab Herbst unseren Kunden an“, sagte Struth. Der Fachöffentlichkeit wird das IoT Gateway zur Messe sps ipc drives im November vorgestellt.
Schon nach 18 Monaten amortisiert
Im Bosch-Werk Homburg haben Ingenieure mit dem IoT Gateway zum Beispiel einen Prüfstand für Hydraulikventile aus dem Jahr 2007 vernetzt. Dank neuer Sensoren, die die Qualität des eingesetzten Öls überwachen, lässt sich der Zeitpunkt für den nötigen Ölwechsel nun weitaus genauer bestimmen als zuvor. Dies spart Zeit, Geld und schont die Umwelt.
In diesem konkreten Fall hatte sich das Nachrüsten mit dem IoT Gateway bereits nach 18 Monaten amortisiert. Im nächsten Schritt sollen 22 weitere Prüfstände und später viele weitere Maschinen bei Bosch nachgerüstet werden. Außer dem Gateway bietet Bosch auch die nötige Software an, um Daten zum Beispiel in der Bosch IoT Cloud zu analysieren, aufzubereiten und darzustellen.
Das IoT Gateway kommt ohne Programmierung aus
Das IoT Gateway wird – je nach Anwendung – um Sensoren erweitert, die an der nachzurüstenden Maschine angebracht werden. Die Sensoren erfassen etwa Temperatur, Druck, Vibration, Stromverbrauch, Ölqualität, Neigungswinkel, Drehgeschwindigkeit oder andere Parameter. Diese Daten übersetzt die Software in Echtzeit in ein Format, das sich in bestehenden Produktionsumgebungen eingliedern lässt – „wie ein nimmermüder Simultanübersetzer für die Industrie 4.0“, sagte Struth.
Das IoT Gateway muss hierfür nicht programmiert, sondern über einen Browser lediglich konfiguriert werden. Das verkürzt die Inbetriebnahme drastisch. Hierbei nutzt Bosch unter anderem die kürzlich präsentierte, neue und offene Maschinensprache PPMP (Production Performance Management Protocol).
Höhere Qualität, rechtzeitige Wartung
Die museale, nun „Industrie 4.0-getunte“ Drehbank ermöglicht wesentliche neue Merkmale der vernetzten Fertigung. Zum einen die Prozessüberwachung für die ständige Qualitätssicherung, zum anderen die fortlaufende Zustandsüberwachung („condition monitoring“), um ungeplante Ausfallzeiten zu verhindern. Für die Prozessüberwachung erfassen Sensoren unter anderem die Drehzahl des Werkstücks: Zu hohe oder zu niedrige Schnittgeschwindigkeiten verschlechtern die Fertigungsqualität beim Drehen von Metall und können das Werkzeug beschädigen. Dank der von Sensoren am IoT Gateway erfassten und übertragenen Daten erkennt der Bediener am Fußpedal jederzeit auf einem Monitor, ob er schneller oder langsamer treten muss, um die optimale Drehzahl einzuhalten.
Zudem erkennt die jetzt vernetzte Drehbank schleichende Veränderungen am Antrieb: Mit zunehmendem Alter kann der lederne Treibrieben zwischen dem Antriebsrad und der Spindel mit dem Werkstück durchrutschen. Für das menschliche Auge ist dieses zunächst unsichtbar. Sensoren erkennen aber bereits Abweichungen im Prozentbereich. Ist ein vorgewählter Schwellenwert erreicht, zum Beispiel ein Durchrutschen von zwei Prozent, sendet das vernetzte System automatisch eine Nachricht an den richtigen Instandhalter. Der wechselt den Riemen innerhalb einer vorgegebenen Zeit aus. So verhindern die Sensoren, das Gateway und die Software den ungeplanten Ausfall der jetzt Industrie 4.0-fähigen Drehbank. Dies steigert die Produktivität.
(st)