Umweltgerecht verpacken mit SiOx-Hochbarriere
Plasmagestützte Oberflächenfunktionalisierung für Mono-Kunststoffe
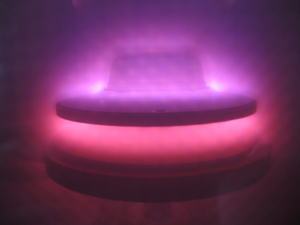
Ansicht eines Bechers im Beschichtungsverfahren.
Quelle: PLASMA ELECTRONIC GmbH/ BARRIOPAC®
Anlässlich der diesjährigen FachPack in Nürnberg präsentiert die Firma PLASMA ELECTRONIC GmbH als Maschinenbauer und Verfahrensentwickler gemeinsam mit BARRIOPAC® detaillierte Informationen zur plasmagestützten Oberflächenfunktionalisierung von Kunststoffprodukten. Diese technisch ausgereifte und im Markt zunehmend etablierte Veredelung von Monomaterialien (Polypropylen/PP, PET oder rPP bzw. rPET) mit einer SiOx-Hochbarriere stellt eine wirksame Alternative zu bisherigen Mehrkomponenten- oder Mehrschichtverpackungen mit Sperrschichten dar. Ebenso wie für Folien (Ceramis®/Amcor) oder Getränkeflaschen (Fresh Safe PET®/KHS), die bereits seit einigen Jahren von verschiedenen Marktteilnehmern teilweise mit SiOx-Schichten beaufschlagt werden, sichert die chemisch inerte Beschichtung die qualitativ hochstehenden Eigenschaften von Bechern, Behältern oder Kapseln.
Angesichts der sich abzeichnenden Marktforderungen und gesetzlichen Vorgaben mit Blick auf Kreislaufwirtschaftsmodelle, Abfallvermeidung, werkstoffliches Recycling, CO2-Reduktion und recyclingfreundliches Verpackungsdesign, stellen die Partner PLASMA ELECTRONIC GmbH/BARRIOPAC® ihr Verfahren zur Erzeugung von Barriereverpackungen den heute gängigen Lösungen entgegen.
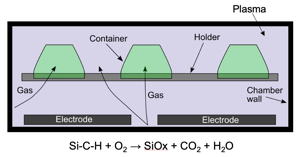
Schematische Übersicht über das PECVD-Verfahren (Plasma Enhanced Chemical Vapour Deposition).
Quelle: PLASMA ELECTRONIC GmbH/ BARRIOPAC®
Becher, Schalen oder Kapseln für Produkte, die sehr gute Barrierewerte bezüglich Sauerstoff, Schutzgasen, Wasserdampfpermeation, ätherische Öle und Aromen bieten müssen, können dank der Plasmabeschichtung im Kern aus Monomaterial, auch recycelter Ware, gefertigt werden. Das Ergebnis ist ein Monomaterial mit einer SiOx-Barriereschicht. Lange Haltbarkeitszeiten, wie sie für einzelne Lebensmittel gefordert sind, können so bei vollem Erhalt der Qualität erzielt werden. Eine weitere Eigenschaft der plasmabeschichteten Packmittel ist die minimierte Wechselwirkung von Packstoff zu Produkt, von Produkt zu Packstoff.
Das Verfahren erlaubt umweltverträgliche und hochwertige Lösungen für anspruchsvolle Produkte. So sind bereits vielfältige Anwendungen der Plasmatechnologie im Niederdruck industriell etabliert. Mit den möglichen Materialkombinationen geht eine Reduktion des Carbon Footprint einher, die die klimatischen Auswirkungen der Herstellung der Packstoffe begrenzen.
Der Ansatz von PLASMA ELECTRONIC GmbH/ BARRIOPAC® heißt, wo immer möglich von Mehrschichtverbunden aus vielfältigen Kunststoffen auf Monomaterialien mit einer hauchdünnen, inerten Barriereschicht umzusteigen. So entstehen Verpackungen, die als hochwertiges Rezyklat für die rohstoffliche Verwertung vorteilhaft sind.
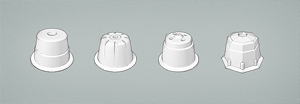
Das Beschichtungsverfahren eignet sich für diverse Geometrien der zunehmend nachgefragten Kapseln für Kaffee, Tee oder andere Getränke.
Quelle: PLASMA ELECTRONIC GmbH/ BARRIOPAC®
Die Becher oder Behälter (hergestellt im Thermoform- oder Spritzgießverfahren) werden in eine Kammer geführt. Dort wird ein Vakuum erzeugt und anschließend siliziumhaltiges Gas und Sauerstoff eingeleitet. Mittels der Elektrode wird das Plasma erzeugt. Dann erfolgt der schichtweise Aufbau der Beschichtung.
Kunststoffbehälter aus Monomaterialien mit einer inerten, transparenten, lebensmittelechten Beschichtung – die Technologie verbindet den Spritzguss wie auch das Tiefziehen mit einer Plasmabeschichtung die auf verschiedenste Behältergeometrien aufgebacht werden kann.
Die Monomaterialbecher mit der Beschichtung auf der Innen- und Außenseite weisen sowohl mit Blick auf Aromen, Sauerstoff und Geschmack des Füllgutes viel bessere Barriereleistungen auf, als es die meisten derzeitig eingesetzten Kunststoffverpackungen zu leisten vermögen. Die funktionelle Barriere beispielsweise auf dem PP-Becher sichert dem Füllgut neben der hervorragenden Qualitätsbewahrung zugleich auch ein längeres shelf-life.
PLASMA ELECTRONIC GmbH/BARRIOPAC® auf der FachPack 2019: Halle 8, Stand 8-402
(st)