Flexodruck am Wendepunkt
Digitalisierung und Automatisierung entscheiden über die Zukunft des Flexodruckprozesses
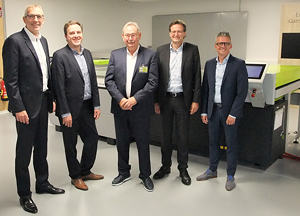
Führten beim Presse-Workshop anlässlich des 25-jährigen Jubiläums ihrer Zusammenarbeit eine interessante Diskussion auf hohem Niveau (von links nach rechts): Markus Gehler, Pascal Thomas, Udo Linke, Dr. Thomas Klein und Antoin Daamen.
Quelle: ESKO
Wie muss der Flexodruck weiterentwickelt werden, um seine herausragende Position im Verpackungsmarkt langfristig abzusichern? Esko und die Warburger Klischee Anstalt teamwka nahmen das 25jährige Jubiläum ihrer Partnerschaft zum Anlass, diese Frage im Rahmen eines Presse-Workshops zu diskutieren. Die interessante Veranstaltung fand am 19. Oktober 2021 im Kundenerlebnis-Zentrum von Esko in Itzehoe in Schleswig-Holstein statt.
Im Laufe von mehr als zwei Jahrzehnten enger Zusammenarbeit haben Esko und teamwka eine Reihe wegweisender Innovationen für den Flexodruck zur Marktreife gebracht. „teamwka arbeitet als einer der marktführenden Druckformhersteller für Top-Unternehmen der Markenartikelindustrie und ist damit für unsere Produktentwicklung ein idealer Partner“, unterstrich Dr. Thomas Klein die Bedeutung der Partnerschaft für Esko. Neben dem CTO Hardware nahmen mit Pascal Thomas, Director Flexo Business, Antoin Daamen, Regional Business Director Central, Markus Gehler, Business Development Manager Flexo für Deutschland, Österreich und die Schweiz, sowie Jan Buchweitz, Product Manager Digital Flexo, vier weitere Flexodruck-Experten von Esko an dem Presse-Workshop teil.
„Wir müssen aufpassen, dass wir den Zug nicht verpassen. Insbesondere der Digital- und der Offsetdruck sind uns beim Workflow meilenweit voraus. Zumindest teilweise inzwischen auch der Tiefdruck. Der Flexodruck dagegen leistet sich nach wie vor einen zerstückelten Workflow mit vielen manuellen Arbeitsschritten, wie es sie in keinem anderen Druckverfahren mehr gibt“, legte Udo Linke, Geschäftsführender Gesellschafter von teamwka und des Schwesterunternehmens teamkind, den Finger in die Wunde. Getreu dem Motto „Brand meets Print“ decken beide team-Unternehmen mit drei Produktionsstandorten in Warburg, Bielefeld und Enschede in den Niederlanden alle Anforderungen ihrer Kunden an die Repro sowie die Herstellung von Druckformen und Klischees für den Flexo-, den Tief-, den Offset- und den Becherdruck aus einer Hand ab. Mit einer Einschränkung: Die Daten für die Tiefdruckzylinder-Gravur übergeben sie an externe Dienstleister.
First time right
Durchgängige Digitalisierung, Automatisierung und Integration der Arbeitsschritte – so sieht Linke auch im Flexodruck den Prozess der Zukunft: „Der Flexodruck braucht harmonisierte und integrative Workflows in einem technisch anspruchsvollen Umfeld. Wir müssen die Medienbrüche im Flexo-Vorstufen-Workflow ausmerzen und auf Anhieb zuverlässig einwandfreie Druckformen sowie Verpackungen herstellen können. Das Ziel muss heißen: First time right.“
Also eine Null-Fehler-Produktion, die in der Druckvorstufe beginnt, indem sie vor allem die bislang noch offene Lücke zwischen der Reproduktion und der Druckplattenherstellung schließt.
Linke: „Hier wird die Schlacht geschlagen. Den Markenartikelherstellern ist es letztlich egal, mit welchen Druckverfahren und welchen Druckplatten ihre Verpackungen produziert werden. Hauptsache, die Qualität stimmt, und ihre Verpackungen werden schnell geliefert.“ Alleine schon der zunehmende Fachkräftemangel in den Druckereien mache es notwendig, im Flexodruck integrierte, standardisierte Workflows zu entwickeln.
Quo vadis Flexodruck?
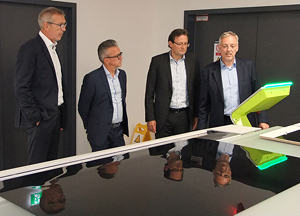
Markus Gehler, Antoin Daamen, Dr. Thomas Klein und Jan Buchweitz (von links nach rechts) bei der Demonstration des neuen CDI Crystal 4260 XPS mit integrierter Bebilderungs- und Belichtungseinheit.
Quelle: ESKO
In den Diskussionen des Presse-Workshops wurde immer wieder die einzigartige Flexibilität des Flexodrucks betont. Kein anderes Druckverfahren kann eine solch breite Palette unterschiedlicher Materialien in hoher Qualität bedrucken. Auch neue nachhaltige Verpackungsmaterialien sind für den Flexodruck keine Herausforderung. Eine Vielseitigkeit, die gleichzeitig Fluch und Segen ist – müssen doch die vielen Möglichkeiten im Workflow abgebildet werden können. Und das bei großen Verpackungsgruppen in weltweit hunderten Werken. „Wir entwickeln unsere Produkte so, dass sie sowohl für Europa als auch für andere Teile der Welt wie unter anderem Asien oder Amerika passen. Indem wir unsere Lösungen adaptierbar halten und sie gleichzeitig integrierbar machen, gelingt es uns, die Komplexität zu strukturieren“, beschrieb Daamen die Philosophie, mit der Esko den unterschiedlichen Anforderungen gerecht wird.
„Der gesamte Flexoprozess muss von der Reproduktion bis zur Druckmaschine konsistenter werden. Das erreichen wir nur, indem wir die verschiedenen Parameter digital fixieren und damit wiederholbar machen. Und wir müssen die manuellen Arbeitsschritte mit ihren Fehlerpotenzialen aus dem Prozess eliminieren“, formulierte Klein die Herausforderung. Als Beispiel sprach Thomas mit CrystalCleanConnect die auf der diesjährigen virtual drupa von Esko und Asahi Photoproducts gemeinsam präsentierte Neuentwicklung für die vollautomatische Herstellung von Flexodruckplatten an. Diese Innovation reduziert die Zahl der Produktionsschritte im Plattenherstellungsprozess von zwölf auf einen.
„Vor 20 Jahren haben wir im Offsetdruck mit der automatischen Übergabe von Daten in die Farbzonensteuerung experimentiert. Heute ist sie Standard. Mittlerweile entscheiden in manchen Digital- und Offsetdruckereien bereits die MIS-Systeme, auf welchem Weg und wo die Druckerzeugnisse produziert werden. Im Flexodruck wird das auch so kommen“, blickte Gehler in die Zukunft.
Hohe Prozesseffizienz
Um die individuellen Anforderungen seiner Kunden flexibel und effizient abdecken zu können, hat Linke für seine Unternehmen vor vielen Jahren die Entscheidung getroffen, eigene Software-Lösungen zu entwickeln. So hat seine IT-Abteilung ein web-basiertes MIS namens teamflow für das Daten-Management und mit teamshare ein Portal für die Kommunikation mit Kunden bis hin zum digitalen Proofing geschaffen. Über diese Systeme fließen alle für den Druck relevanten Parameter wie unter anderem die Druckkennlinien oder die Farbdaten unmittelbar in die Reproduktion und in die Herstellung der Druckformen ein.
Ein ebenfalls eigenentwickeltes Dashboarding ermöglicht den Kunden über das Internet detaillierte Einblicke in die Produktion bis in die Druckmaschinen hinein. Unter anderem visualisieren diese Übersichten in grafisch ansprechender Form und leicht verständlich vordefinierte Leistungskennzahlen. So können die Kunden zum Beispiel die Freigabeprozesse und Artwork-Revisionen für Prozessverbesserungen analysieren.
„Zunächst lassen wir uns von den Markenartikelherstellern ihre Arbeitsweise erklären. Anschließend bilden wir ihre Produkte in unserem Workflow-Management so ab, wie sie es benötigen. Zum Beispiel für einen Hersteller von Tiefkühlkost haben wir in unseren Systemen etwa 35 Modelle angelegt, weil bei seinen Produkten jeweils unterschiedlich gearbeitet wird“, berichtete Linke. Bei Bedarf können die Modelle, die letztlich die Prozesse der Kunden standardisieren, flexibel angepasst werden. Die Parameter der Produktion werden einmal im System erfasst und stehen in allen Arbeitsschritten zur Verfügung. Sowohl die beiden team-Unternehmen als auch die Kunden sparen Zeit und arbeiten kosteneffizient.
Die 100%-Druckinspektion wird integriert
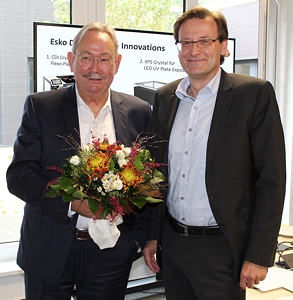
Freuen sich über 25 Jahre partnerschaftliche Zusammenarbeit: Udo Linke (links) und Dr. Thomas Klein.
Quelle: ESKO
Im Rahmen ihrer Partnerschaft arbeiten beide Unternehmen aktuell an der Integration des AVT-AutoSet-Moduls der Esko Automation Engine für die 100%-Druckinspektion in den Workflow der team-Unternehmen. Dieses Projekt verfolgt das Ziel, neue Möglichkeiten für die Automatisierung der Einstellprozesse und die Standardisierung der Qualitätssicherung zu eröffnen, indem die Auftragsdaten und die Daten für die 100%-Druckinspektion automatisch aus der Druckvorstufe in die Qualitätskontrolle der Druckmaschinen bzw. der Rewinder fließen.
Für jeden Job wird ein „Inspection Package“ angelegt, das jeweils aus JDF-, TIFF- und PDF-Dateien besteht. Die JDF-Dateien enthalten neben den Job-Informationen die Koordinaten der Inspektionsbereiche sowie die im MIS hinterlegten LAB-Farbwerte der definierten Farbmesspunkte. Die Koordinaten der Inspektionsbereiche werden unter anderem in der Projektentwicklungs-Software PackEdge und dem nativen PDF-Editor ArtPro+ festgelegt. Beides sind Lösungen von Esko. Die TIFF-Bilddateien dienen als Referenz für den Abgleich der Inspektionsbereiche und die PDF-Dateien als Referenz für den Abgleich der Druckbilder. Die Inspection Packages werden gezippt an die Qualitätssicherung übergeben. Später können die AVT-Kamerasysteme wie zum Beispiel Argus Turbo HD die zu prüfenden Bereiche automatisch anfahren.
Ein Integrationsschritt, der die Rüstzeiten bei Auftragswechseln im Flexodruck weiter verkürzt, da in der Qualitätssicherung manuelle Eingaben wegfallen. Während das manuelle Einstellen der Qualitätssicherung durchschnittlich etwa sieben Minuten beansprucht, ist sie mit AVT AutoSet bereits nach 40 Sekunden vorbereitet. Darüber hinaus schließt die automatische Datenübergabe Fehlerquellen aus, die dort lauern, wo Maschinenführer die Daten für die Qualitätskontrolle neu erfassen müssen. „Zudem stellt diese Integration sicher, dass die Inspektion unabhängig vom ‚Faktor Mensch‘ stets in der erforderlichen Weise ausgeführt wird“, ergänzte Klein.
Durchgängige Farb-Workflows
Inzwischen ermöglicht Esko seinen Kunden die Realisierung eines kompletten Farb-Workflows einschließlich Farbmanagement: Erst kürzlich hat das Unternehmen X-rite ColorCert inline mit AVT SpectraLab XF verbunden. Das heißt, die Qualitätssicherung lässt sich bis hin zur Inline-Spektralfarbmessung ausbauen. „Es gibt inzwischen erste Installationen, bei denen die AVT-Systeme innerhalb eines bestimmten Rahmens sogar die Druckmaschinen steuern, indem sie zum Beispiel die Beistellungen und Passer korrigieren“, beschrieb Klein, wie weit sich der Prozess integrieren lässt.
„Wir machen heute alle unsere Testformen AutoSet-fähig – unabhängig davon, ob AutoSet auf den Druckmaschinen installiert ist, mit denen die Verpackungen unserer Kunden gedruckt werden“, erklärte Linke.
Das breite Angebot lässt Kunden alle Optionen
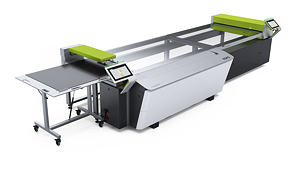
Mit der neuen Crystal-Technik von Esko wird die Herstellung von Flexodruckplatten einfach und sicher wie nie zuvor.
Quelle: ESKO
In seinem Kundenerlebnis-Zentrum in Itzehoe hat der Geschäftsbereich Flexoplattenherstellung von Esko seine Forschung, Produktentwicklung und seinen Maschinenbau für den Flexodruck unter einem Dach angesiedelt. Hier präsentiert das Unternehmen unter anderem seine neue Crystal-Technik. Diese kombiniert die digitale Plattenbebilderung und die UV-Belichtung mit gleichzeitiger Haupt- und Rückseitenbelichtung zu einem automatischen Prozess für die Druckplattenherstellung. Wie komfortabel diese funktioniert, demonstrierte Buchweitz live mit dem neuen CDI Crystal 4260 XPS mit integrierter Bebilderungs- und Belichtungseinheit für Flexodruckplatten mit Größen bis zu 1.067 x 1.524 mm.
Inzwischen sind weltweit mehr als 185 CDI Crystal Flexo-Druckplattenbelichter sowie 330 XPS Crystal UV LED-Belichtungssysteme im Einsatz, darunter 35 mit dem Wechselsystem PlateHandler als vollautomatisierte Systeme. Alle Esko-Maschinen lassen sich über die Automation Engine steuern. Insgesamt umfasst das Portfolio des Unternehmens neun verschiedene CTP-Plattenbelichter für den Flexodruck. „Mit dieser Angebotsbreite sind wir einzigartig im Markt“, stellte Thomas fest.
Für Esko ist die UV LED-Belichtung der entscheidende Faktor für die Qualität der fertigen Druckplatten. Klein: „Wir haben bei Kunden etliche mit UV-Dioden belichtete Druckplatten durch verschiedene Lösemittelprozessoren geschickt und damit festgestellt, dass die Streubreite im Druck bei diesem Prozess im Vergleich zur herkömmlichen Belichtung deutlich zurückgeht. Das heißt, die UV-Belichtung nimmt sehr viel Fluktuation aus dem Prozess heraus.“
Esko zertifiziert alle Druckplatten
Mit dem Ziel, seinen Kunden im Druckprozess höchste Stabilität zu ermöglichen, zertifiziert Esko alle neu auf den Markt kommenden Flexodruckplatten – inzwischen bereits mehr als 150 Platten verschiedener Hersteller. Im Rahmen des aufwändigen Prozesses werden mit den Platten zunächst verschiedene Muster nach DFTA-Standard gedruckt. Im nächsten Schritt analysieren Experten von Esko die Druckergebnisse anhand von mehr als 30 verschiedenen Kenngrößen. Schließlich werden die Parameter der UV LED-Belichtung für jede Druckplatte optimiert und die Ergebnisse in den XPS-Belichter von Esko hinterlegt. Bediener dieser Systeme brauchen den Druckplattentyp, den sie verarbeiten wollen, nur noch im Menü auszuwählen. Anschließend produzieren die XPS-Belichter die Druckplatten automatisch anhand der hinterlegten Parameter. Damit stellt Esko sicher, dass die Druckplatten bei Kunden optimal verarbeitet werden und sie im Druck einwandfreie Ergebnisse liefern.
Nähe zu den Maschinenführern
teamwka verfügt europaweit eine sehr große Kapazität in der Herstellung digital gelaserter Druckplatten. Bislang hat das Unternehmen insgesamt 15 CDI-Laserbelichter – darunter einen Belichter speziell für den Becherdruck – und acht Upgrades von Esko gekauft. Allein in diesem Jahr wurden drei ältere Systeme gegen neueste CDI-Technik ausgetauscht.
„Alle am Prozess beteiligten Seiten müssen die Dinge vor ihrer Haustüre in Ordnung bringen. Mit den Druckereien, mit denen wir zusammenarbeiten, haben wir das gemeinsam getan. Das erklärt die extrem hohe Quote einwandfreier Druckplatten und Druckergebnisse, die wir europaweit produzieren“, meinte Linke. „Wir haben stets die Nähe zu den Druckern gesucht und wollen sie auch künftig einbeziehen. Die Maschinenführer müssen die Vorteile der Digitalisierung und Automatisierung – kürzere Rüstzeiten und höhere Sicherheit im Druck – für sich erkennen.“
(kb)