safe and robust bottles in numerous designs, shapes and colors
BASF expanded its Ultrason® P portfolio
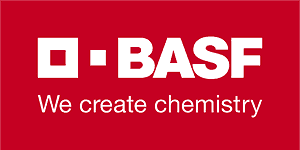
Quelle: BASF
BASF has now expanded its Ultrason® P portfolio so that it can be used to manufacture high-quality bottles by all three processing methods that are standard in the industry. The two polyphenylsulphone (PPSU) grades Ultrason® P 2010 and P 3010 can be used in injection stretch blow molding, extrusion blow molding and injection molding to manufacture bottles for adults and babies that are safe to use, robust and chemically resistant as well as available in numerous designs, shapes and colors.
All three processing methods benefit from the customized properties of the high-temperature thermoplastic: It contains no harmful substances, is approved for food contact and has outstanding strength, chemical resistance and long-term high-temperature stability up to 180°C. Bottles made from the transparent, slightly honey-colored BASF polyphenylsulphone can easily withstand sterilization in a microwave or in very hot water – regardless of the method used to manufacture them.
“The production of high-quality, safe and stylish bottles for adults and babies presents a challenge that cannot be compared to that of conventional PET, PP or co-polyester bottles,” says Georg Grässel from BASF’s global business development Ultrason®. “The globally widespread processing methods all have their own specific requirements of the material used – and this is where Ultrason® P has proven its value to customers in many different countries. They can choose the most suitable material from our portfolio and can also benefit from our on-site technical application support and the global availability of the different grades.”
During extrusion blow molding, the plastic melt is extruded from top to bottom through a circular die to form a tube-shaped parison. Internal pressure is then used to inflate the parison within a mold thus giving the part its shape. The medium- viscosity Ultrason® P 3010 is particularly suitable for this process due to its inherent high melt strength in contrast to other PPSU materials on the market. This allows the hot, elongated parison to remain stable even near the die, ensuring uniform blow molding. For complex geometries with different wall thicknesses and designs, a programmed parison control can be used. This prevents elongation of the parison caused by the parison’s weight and results in uniform wall thicknesses over the complete length of the bottle.
When injection molding is used, the bottle body can be injection molded with or without a cap thread and base, which provides great flexibility when it comes to the bottle design or the method used to vent baby bottles. Today, the manufacturing with single and multi-cavity molds in combination with an upstream hot runner system is state of the art. The high-flow, low-viscosity Ultrason® P 2010 is particularly well suited for this, as it makes thin walls possible even when there are long flow paths – without compromising the impact or chemical resistance.
Ultrason® is the trade name for BASF’s product range of polyethersulfone (Ultrason® E), polysulfone (Ultrason® S) and polyphenylsulfone (Ultrason® P). The high- performance material is used to manufacture lightweight components in the electronics, automotive and aerospace industries as well as in water filtration membranes and in parts that come into contact with hot water and food. Because of their extraordinary property profile the Ultrason® brands can substitute thermosets, metals and ceramics in many applications.
With more than 110,000 employees, the BASF Group generated sales of €59 billion in 2020, including the Performance Materials division achieving global sales of €5.63 billion.
(kb)