Gerhard Schubert GmbH strengthens its pioneering role in packaging technology during the 2020 pandemic year
Cautious leadership management during the Corona crisis is paying off
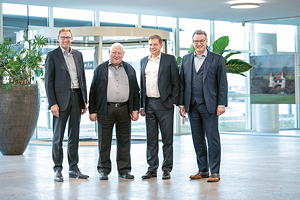
Schubert’s corporate management: Marcel Kiessling, Managing Director Sales and Service, Gerhard Schubert, Founder and Managing Partner, Ralf Schubert, Managing Partner, Peter Gabriel, Commercial Managing Director (from left to right)
Quelle: Gerhard Schubert GmbH
Despite the extraordinary challenges the world faced during the 2020 financial year, packaging machine manufacturer Gerhard Schubert GmbH posted a positive business result that was significantly better than the Corona-related forecast adjustments at the beginning of the pandemic year suggested. The Schubert Group achieved an increase in turnover of 2.5 per cent in the 2020 financial year, representing a total of 281 million euros in sales, therefore confirming the cautious management and dedicated commitment of all 1450 employees during the Corona crisis. The order position also developed very positively. Driven by growth in the USA and Europe, Schubert realised a 25 per cent increase in incoming orders compared to the previous year.
In the unforeseen pandemic situation and at an early stage, the Crailsheim-based world market leader in packaging technology relied on a company-internal task force along with a comprehensive safety and hygiene concept. “It was a very good decision and is still working very well for us today. Thanks to the measures implemented to minimise the impact of COVID-19 on our operations, we have a very low number of employees who fell ill overall. We have been and continue to be able to work and deliver to our customers at all times,” explains Peter Gabriel, Commercial Managing Director of Gerhard Schubert GmbH.
Digital services prove their worth
The manufacturer is benefiting from the fact that it is well advanced in the field of digitalisation. “Our capabilities for virtual machine approvals, AR-supported service processes and digitally supported commissioning at customer sites have naturally proven very successful in customer support in 2020 and will continue to be an important focus of our development in the coming years,” reports Marcel Kiessling, Managing Director Sales and Service. In this context, the increases in service revenues compared to the previous year are clear: In spite of all the restrictions on travel and availability of service staff, Schubert achieved an increase in turnover in this key area from 54 (2019) to 59 million euros. This is just one reason why the further development of service offerings is an integral part of the company’s growth strategy: “A key focus is to increase and optimise performance tracking. Added to this is the customisation of our services – flexible and ideally adapted to specific customer requirements,” continues Kiessling.
Innovations with international growth potential
International growth, especially in the USA and Europe, is currently being driven by the manufacturer’s immediately available and preconfigured lightline machine series, which enables customers to react quickly to market trends, along with significant advances in the development of tools for process optimisation using predictive maintenance (GRIPS.world). The establishment of industrial on-demand 3D printing processes for additive manufacturing in both plastics and metal, along with the consistent further development of sustainable packaging solutions and a strong focus on consulting, are all additional success factors behind Schubert’s current development. Business in the USA developed very positively in this context. The Schubert subsidiary generated around 82 million US dollars in sales in North America in 2020. In addition to upward trends at Schubert UK and the main European markets of France and Italy, the Polish market is also becoming increasingly important for the manufacturer.
The future is both sustainable and flexible
Ground-breaking innovations and investments enable Schubert to continue winning over customers, while strengthening the company’s leadership position in the industry during the 2020 pandemic year. Ralf Schubert, Managing Partner explains: “We have been intensifying our research activities in the field of robotics technology for some time. With AI projects in the field of robotics and image processing, we are making a decisive contribution to the ongoing professionalisation and future viability of the entire packaging industry. Added to this is the development of innovative assemblies for our TLM machines as well as our first collaborative robot and progress on TITAN, our packaging systems’ digital twin.” To this end, the Crailsheim-based company has been investing around 8 to 10 per cent of its annual turnover for decades in a time-tested tradition.
It is also thanks to this innovative strength that Schubert is able to continuously expand its trailblazing role in the automation of sustainable production processes and in the development of innovative packaging materials. “The future belongs to environmentally friendly packaging materials such as cardboard trays or fibre-based films which can be used flexibly on a packaging line. Our customers benefit from over 50 years of Schubert experience in cardboard packaging along with our consulting and service expertise," says Marcel Kiessling.
Outlook for 2021
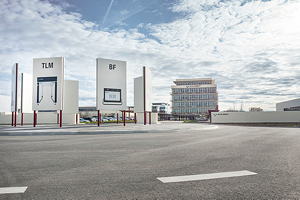
With the successful completion of the relocation of the L2218 state road on 9 April 2020, Gerhard Schubert GmbH laid the foundations for the planned expansion of the site on the newly acquired land.
Quelle: Gerhard Schubert GmbH
Supported by the high order backlog and equally positive order intake in the first quarter, Schubert is very confident about the development of the current financial year: “Our production capacities are currently very well utilised. We already have 100 per cent of the planned annual turnover in our order books for 2021 and are already planning our new orders into 2022,” says Peter Gabriel, describing the favourable situation. The signs are pointing towards continued growth for the manufacturer in other respects too; In the second half of 2021, construction of the new assembly hall will begin as part of the planned further expansion of the Crailsheim site. Prior to this, in 2019 the adjacent country road was rerouted in order to make way for the extensive construction work, creating the necessary space and ideal conditions for up to 300 additional employees.
Gerhard Schubert GmbH is a globally recognised market leader in top-loading packaging machines (TLM). For its digital, robot-based packaging machines, the family-owned company based in Crailsheim (Baden-Württemberg, Germany) builds on an interplay of simple mechanics, intelligent control technology and high modularity. With this philosophy and a highly developed culture of innovation, the company has been pursuing an entirely independent technological path for more than 50 years.
With its TLM technology, the machine manufacturer provides its customers with future-proof packaging machine solutions that are easy to operate, flexible in terms of format conversion, high-performance and stable in function. The TLM packaging machines pack products of all types and from all sectors – from food, confectionery, beverages, pharmaceuticals and cosmetics to technical products – into trays, cartons, boxes or into flow-wrap bags.
Well-known brands such as Ferrero, Nestlé, Unilever, Mondelez and Roche rely on Schubert’s automation solutions, as do numerous small, medium-sized and family-owned companies. Founded in 1966, the second generation of the company now employs 1,400 people.
(kb)